1. Newcomers Must Know! Precautions and Common Error Avoidance in Operating the 4 Side Sealing Bag Packing Machine
If you're new to operating the 4 Side Sealing Bag Packing Machine, there's a wealth of knowledge to absorb to ensure smooth and efficient operations. This machine, a staple in the packaging industry, can seem intimidating at first, but with the right guidance, you'll be operating it like a pro in no time.
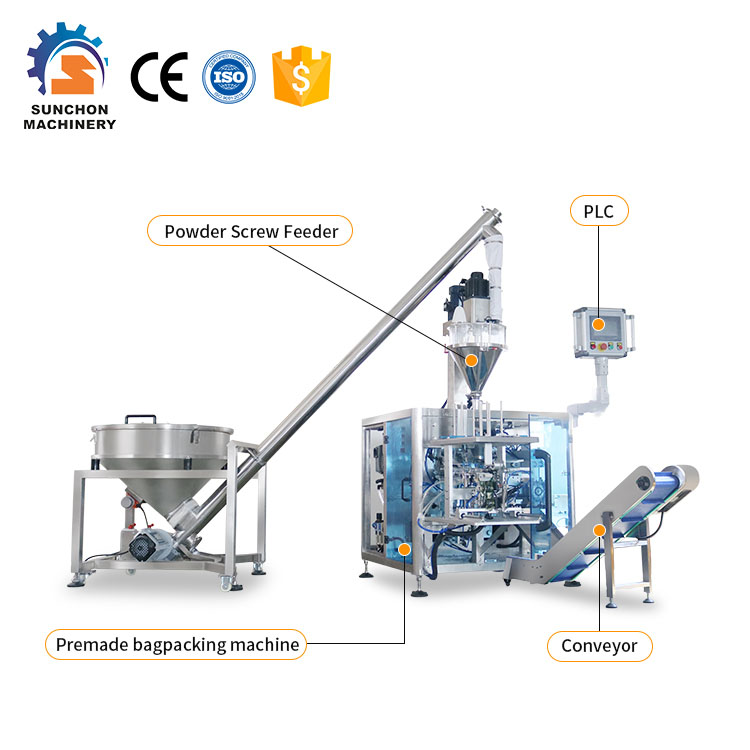
Initial Pre - operation Checks
Before powering on the 4 Side Sealing Bag Packing Machine, a series of meticulous checks are essential. First and foremost, the power supply demands your attention. Ensure that the voltage and frequency match the machine's specifications. A mismatch can lead to electrical failures, which not only disrupt the production process but can also damage the machine's delicate components. For example, if the machine is designed to operate at 220 volts and is connected to a 110 - volt supply, it may not function properly, and the motor could overheat due to insufficient power.
Inspecting the packaging materials is another crucial step. The bags you intend to use must be of the correct size, shape, and material. The width, length, and thickness of the bags should align with the machine's settings. If the bags are too narrow, they may not feed properly through the machine, causing jams. Incorrect material selection can also pose problems. For instance, using a film that is not heat - sealable with the machine's sealing mechanism will result in ineffective sealing.
Cleanliness is next on the list. A dirty machine is a breeding ground for issues. Remove any dust, debris, or leftover product from the previous operation. Dust can accumulate in the moving parts, causing increased friction and wear. Leftover product can contaminate the new batch and affect the quality of the packaging. Use a soft, dry cloth to wipe down the exterior and a compressed air blower to clean hard - to - reach areas inside the machine.
During - operation Vigilance
Once the machine is up and running, continuous monitoring is key. The running speed of the machine should be stable. Drastic or frequent speed changes can have a domino effect on the packaging process. For example, if the speed is increased suddenly during the filling stage, it may cause the product to spill or the filling to be uneven. On the other hand, a sudden slowdown can lead to inconsistent sealing as the heat and pressure application times are disrupted.
The temperature settings for the sealing process are extremely sensitive. Different packaging materials, such as polyethylene (PE), polypropylene (PP), or polyester (PET), require specific temperature ranges for optimal sealing. PE, for example, typically seals well at a lower temperature compared to PET. If the temperature is set too low for a particular material, the seal may be weak, leading to product leakage. Conversely, if it's too high, the material may melt or deform, ruining the packaging.
Common Errors and Their Remedies
Sealing Problems: One of the most prevalent issues is related to sealing. An incomplete or weak seal can be a nightmare for any packaging operation. Incorrect temperature settings are often the culprit. If the temperature is not calibrated correctly, the heat - activated adhesive on the packaging material may not bond properly. To fix this, refer to the machine's manual for the recommended temperature range for your specific packaging material and adjust the settings accordingly.
Dirty seal bars can also cause problems. Over time, residue from the packaging material can build up on the seal bars, preventing them from making proper contact with the bags. This results in a weak or uneven seal. Regularly clean the seal bars using a mild detergent and a soft brush. Make sure to turn off the machine and let the seal bars cool down before cleaning to avoid any accidents.
Improper pressure during sealing is another factor. If the pressure is too low, the seal may not be tight enough. On the other hand, excessive pressure can damage the packaging material. Check the pressure adjustment mechanism, which is usually located on the machine's control panel or near the sealing unit. Calibrate the pressure to the recommended level based on the thickness and type of the packaging material.
Filling Errors: Uneven filling or over - filling/under - filling can occur due to a malfunctioning filling system. A clogged filling nozzle is a common cause of uneven filling. Small particles of the product can accumulate in the nozzle, restricting the flow. To solve this, disassemble the nozzle and clean it thoroughly. You can use a small brush or a pipe cleaner to remove any debris.
An inaccurate weighing device, if the machine is equipped with one, can lead to over - filling or under - filling. Regular calibration of the weighing device is essential. Use standard weights to check the accuracy of the device. If the readings are off, adjust the calibration settings according to the manufacturer's instructions.
Mechanical issues within the filling system, such as a worn - out conveyor belt or a misaligned filling mechanism, can also cause problems. Inspect the conveyor belt for any signs of wear and tear. If it's loose or damaged, replace it. Ensure that all the components of the filling mechanism are properly aligned. This may involve adjusting the position of the filling hopper or the product delivery chute.
Training and Continuous Learning
Operating the 4 Side Sealing Bag Packing Machine is not just about following a set of rules; it's also about continuous learning. Take advantage of the training provided by the machine manufacturer. This training usually covers everything from basic operation to advanced troubleshooting. Many manufacturers offer online courses or on - site training sessions.
Join industry forums or groups where you can interact with other operators. Sharing experiences and learning from others' mistakes can be invaluable. You may discover new techniques for optimizing the machine's performance or find solutions to problems that you thought were unique to your operation.
Keep up with the latest technological advancements in the field of packaging machinery. Newer models of the 4 Side Sealing Bag Packing Machine may come with improved features, such as more precise sensors for better quality control or energy - saving technologies. Staying informed can help you make the most of your machine and stay competitive in the market.
2. 4 Side Sealing Bag Packing Machine from an Environmental Perspective: How to Help Enterprises Transform to Green Packaging
In an era where environmental concerns are at the forefront of global discussions, businesses are under increasing pressure to adopt sustainable practices. The 4 Side Sealing Bag Packing Machine can be a powerful ally in an enterprise's journey towards green packaging.
Embracing Environment - friendly Packaging Materials
The 4 Side Sealing Bag Packing Machine is highly versatile when it comes to working with different types of environment - friendly packaging materials. One such option is biodegradable plastic bags. These bags are typically made from plant - based materials like polylactic acid (PLA). PLA is derived from renewable resources such as corn starch or sugarcane. When these bags are discarded, they can decompose naturally in the environment, reducing the burden of plastic waste. The 4 Side Sealing Bag Packing Machine can seal these biodegradable bags with the same efficiency as traditional plastic bags, ensuring product protection while minimizing environmental impact.
Another eco - friendly alternative is recycled paper - based bags. Paper is a renewable resource, and using recycled paper further reduces the demand for virgin paper production. This helps in saving trees and conserving energy. The 4 Side Sealing Bag Packing Machine can handle paper - based bags, whether they are plain or have additional coatings for moisture resistance. The sealing process for paper bags may require some adjustments in terms of temperature and pressure compared to plastic bags, but with proper calibration, the machine can create a secure and durable seal.
Minimizing Packaging Waste
Precision in filling is a key feature of the 4 Side Sealing Bag Packing Machine that contributes to waste reduction. By accurately measuring the amount of product to be packed, the machine helps in eliminating over - filling. Over - filling not only leads to product waste but also requires more packaging material than necessary. For example, in the food industry, if a snack bag is over - filled, the excess product may go to waste, and the larger - than - needed bag uses more resources. The 4 Side Sealing Bag Packing Machine's filling system can be calibrated to ensure that the exact amount of product is dispensed into each bag, optimizing the use of packaging materials.
The machine's efficient sealing system also plays a crucial role in reducing packaging waste. A well - sealed package provides adequate protection for the product without the need for additional layers of packaging. In contrast, a poorly sealed package may require extra wrapping or protective materials to prevent damage during transportation and storage. The 4 Side Sealing Bag Packing Machine's sealing mechanism creates a tight and durable seal, ensuring that the product remains intact throughout its journey from the production line to the end - consumer.
Energy - saving Operation
Energy consumption is a significant concern for any manufacturing operation, and the 4 Side Sealing Bag Packing Machine offers several features to address this issue. Many modern models are equipped with an automatic standby mode. When the machine is not in continuous use, it automatically switches to standby, reducing power consumption. This not only benefits the environment by reducing energy usage but also saves the enterprise money on electricity bills.
Regular maintenance of the 4 Side Sealing Bag Packing Machine is essential for energy - efficient operation. A well - maintained machine runs more smoothly, with less friction in its moving parts. This means that it requires less energy to operate. For example, regularly lubricating the conveyor belts and gears reduces the resistance, allowing the motor to work more efficiently. Additionally, checking and replacing worn - out components, such as belts or bearings, can prevent energy - wasting inefficiencies.
Case Studies of Green Packaging Transformation
Let's take a look at some real - world examples of how enterprises have used the 4 Side Sealing Bag Packing Machine to achieve green packaging transformation. A leading food company decided to switch from traditional plastic bags to biodegradable PLA bags for its snack products. By using the 4 Side Sealing Bag Packing Machine, they were able to seamlessly transition to the new packaging material without sacrificing production efficiency. The machine's ability to handle the unique characteristics of PLA bags, such as their different heat - sealing requirements, allowed the company to meet its environmental goals while maintaining high - quality packaging.
A small - scale organic farming business started using recycled paper - based bags for its produce. With the help of the 4 Side Sealing Bag Packing Machine, they were able to seal the bags securely, protecting the freshness of the fruits and vegetables. The business also noticed a reduction in packaging waste as the machine's precise filling system minimized over - filling. This not only made their packaging more sustainable but also improved their brand image among environmentally conscious consumers.
The Future of Green Packaging with the 4 Side Sealing Bag Packing Machine
As technology continues to advance, the 4 Side Sealing Bag Packing Machine is likely to play an even more significant role in green packaging. Research is being conducted to develop more advanced sensors and control systems that can further optimize the machine's performance in terms of energy consumption and waste reduction. For example, smart sensors may be able to detect the type of packaging material automatically and adjust the machine's settings accordingly, ensuring the most efficient use of resources.
In addition, the development of new and more sustainable packaging materials will continue to drive the evolution of the 4 Side Sealing Bag Packing Machine. As these materials become more widely available, the machine will need to be adaptable to handle their unique properties. This presents both a challenge and an opportunity for manufacturers to innovate and create more environmentally friendly packaging solutions.
In conclusion, the 4 Side Sealing Bag Packing Machine has the potential to be a game - changer in the pursuit of green packaging. By using environment - friendly materials, reducing waste, and operating efficiently, enterprises can make a significant contribution to environmental protection while maintaining their competitiveness in the market.